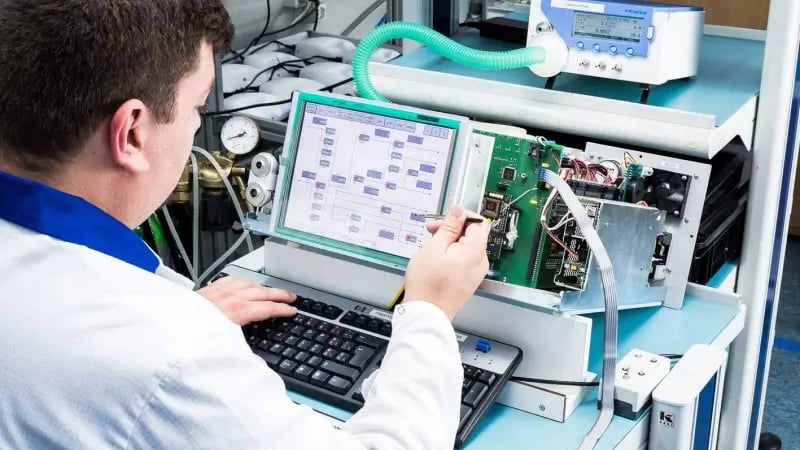
The Twinstream™ Multi Mode Respirator was created with ESCATEC’s custom pneumatic model at its heart.
The respirator blends air (21% oxygen [O2]) and 100% O2 into a gas mixture with a defined O2 concentration accuracy of +/-3%. The embedded pressure controller is also integral for applying accurate pressure to patients with varying lung sizes and elasticity.
The system was designed with safety at the forefront, in accordance with the regulatory standard for medical equipment, ISO 13485.
“We are used to operating to these very exacting standards which are vitally important, as patients’ lives depend on the equipment working correctly all the time.” Daniel Pfeifer, Former Head of Global R&D at ESCATEC
Every safety measure was carefully implemented. An independent microcontroller system supervises all the safety-relevant functions of a second controller system, measuring temperatures, pressures, O2, CO2, electrical voltages and currents. These functions are implemented on a powerful embedded computer with the Windows CE operating system. As this system is not safety-relevant, the patient can still be ventilated in case of breakdown.
The second embedded system is based on a DSP without an operating system to implement all safety-relevant functions while the third, smallest controller can be powered through a 9V battery for use during blackouts.
This end-to-end process, centred on precision and quality, removes the gap between design and manufacture that can typically cause friction. This means that the product could be safely and efficiently optimised for mass production from the outset, keeping costs low and removing unnecessary production delays. Working this way also ensured that Carl Reiner remained in control of design with full IP.
We are very proud to have designed a unique product that is saving lives on a daily basis in many leading hospitals around the world.
