Variously known as the Engineering Change Note, Order or Request (ECN, ECO or ECR), the process for managing changes to the manufacturing data pack for any electronic or electro-mechanical product should be well established within all engineering and manufacturing organisations.
However, it is too often overlooked and sometimes seen as an inconvenient paperwork exercise, at a time when rapid change is required. Satisfying customer demand will of course be a priority, but failing to keep your supporting documentation updated could cause you serious headaches further down the line.
In this post, I will look to provide some best practice advice on implementing a robust ECN process, the controls that are required as part of this process, and the areas that can often be discounted.
Defining an engineering change note
I was taught, many years ago, that an ECN is only an ECN if it’s a change that affects the form, fit or function of a product. As a basic definition that’s fine, however in a manufacturing operation it is not uncommon for the ECN process to cover more than that: for example, changes to the manufacturing or test process, or use of alternative components. This is because the ECN system and the records on file can provide a really good life history of both the development of the product and the processes that affect it - information that can prove to be extremely beneficial.
It is perhaps worth highlighting here the distinction between an ECN and a concession, as they are sometimes confused due to the fact they both follow a very similar process. An ECN is usually a permanent change once implemented, whereas a concession should be temporary, for example covering a set period of time, batch or range of serial numbers. Whilst a good Electronics Manufacturing Services (EMS) provider will be able to manage both variations on your behalf, it’s important to be clear with them from the outset what kind of change you need to make.
And finally, the ECN is an essential part of the communication process between you, the design authority, and your EMS partner. Whether you are outsourcing a printed circuit board assembly (PCBA), box build or complex electro-mechanical assembly, verbal instructions made directly to production staff are no longer an option. It becomes therefore a vital method of passing information between you and your EMS provider – and, of course, vice versa.
Controlling the changes
Many manufacturing software packages now have a means of raising, processing and tracking ECNs, though for critical processes a piece of paper that is physically ‘signed off’ at each stage of acknowledgement can still be effective. Perhaps most importantly, an ECN shouldn’t just be sent on an email that could be accidentally deleted or lie in a junk folder. Any EMS company you are working with must be able to demonstrate how they ensure acknowledgement and feedback once the process is complete, or you may not end up with the product you were expecting.
It is critical that the ECN itself clearly details what changes are to take place. Changes that are hidden away in a bill of materials (BOM) or PCB design, for example, may not get picked up unless they are explicitly referenced in the ECN. An unclear or incomplete ECN may result in the manufacturing process effectively having to start again from scratch to ensure nothing has been missed, which can end up becoming time consuming and costly for both parties. In this case, full engineering and tooling charges might apply, rather than relatively modest – or perhaps zero – cost of implementing changes to existing build equipment or information.
It is also important to be clear when an ECN should be implemented. For example, do you want to apply it to the next batch built, or from a certain date? Do you require any of your existing stock to be modified by your EMS provider? Or in extreme cases, do you need to initiate a product recall?
The missing links
An area that can commonly be disregarded during the ECN process is the up-issuing (or up-revising) of drawings. For an electronic product with some history, it can be confusing for those involved in the outsourcing project to find original product drawings with several separate ECNs attached as this opens up potential for interpretation and the possibility of building product to the wrong specification.
Revising part numbers is equally if not more important, as it signifies a change in the product that then should be linked to the ECN for traceability purposes. Best practice advice suggests that the up-issued part number should be linked to the purchase order raised on your assembly partner and/or their manufacturing works order (and hence the build information), so full traceability is maintained. This information could be vital should quality problems occur later, and it becomes necessary to identify exactly when and where the changes occurred.
So whilst it does take time to raise an ECN and follow a robust process; when considered against the risks and costs of not doing it correctly, hopefully you will agree that it’s a very worthwhile exercise.
Image by Sebastien Wiertz
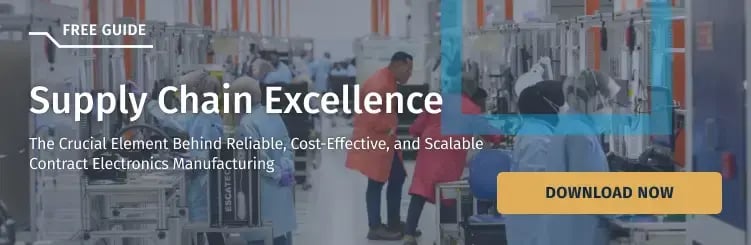